Ведущим предприятием отрасли в Приангарье уже не один десяток лет считается ОАО «Саянскхимпласт» - крупнейший производитель поливинилхлорида в России. И это - несмотря на то, что от своих основных потребителей завод находится за тысячи километров.
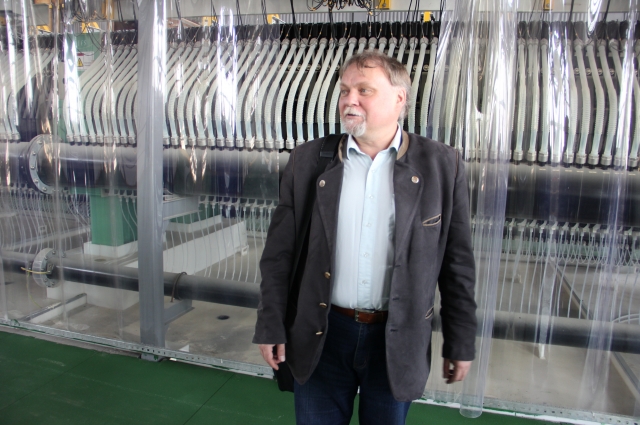
![]() |
---|
Николай Мельник |
- Мы исходим из того, что только постоянно поднимая уровень технической оснащённости, снижая энергозатраты на продукцию, сможем в условиях суровой рыночной экономики не просто выживать, а занимать передовые позиции на рынке, - говорит генеральный директор предприятия Николай МЕЛЬНИК. - Поэтому вся стратегия и тактика нашего коллектива направлена на высокое качество, большие объёмы и непрерывную реконструкцию предприятия.
За последние 10 лет на техническое перевооружение производства саянские химики затратили порядка девяти миллиардов рублей! Не останавливая ни на один день выпуск очень дефицитного в нашей стране поливинилхлорида (ПВХ), они ведут постоянную модернизацию отдельных цехов, блоков и узлов предприятия.
Собственная и уникальная
Формулу «экологичное предприятие выгодно экономически» в Саянске не декларируют, а реализуют. В частности, в 2004 году на заводе приступили к модернизации рассолопромысла. Соль - очень важный компонент для жизнедеятельности не только человека. Без неё не обходится и химическая промышленность, а в производстве ПВХ она является основным сырьём. Чтобы получить его из подземных залежей, в специальные скважины раньше закачивалась вода из реки Ока, которая растворяла соляные пласты, затем насыщенный раствор поднимали на поверхность, соль выпаривали, а оставшийся рассол хранили в огромных бассейнах. Для такой технологии постоянно нужна была чистая вода, огромное количество энергии и громоздкое оборудование.
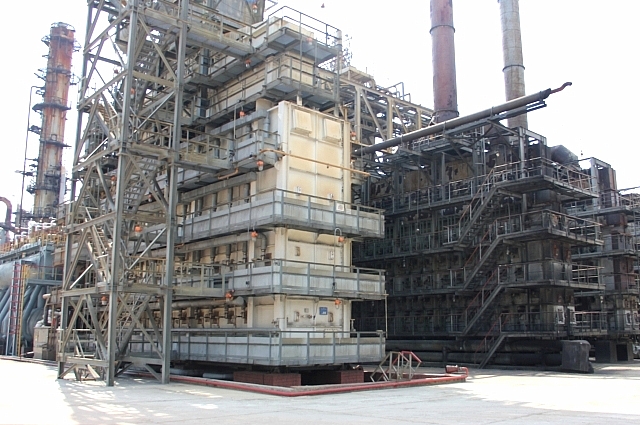
Теперь всё изменилось кардинальным образом: специалисты предприятия разработали свою собственную уникальную бессточную технологию с замкнутым циклом использованных вод.
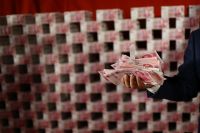
- На первом этапе вода через шахту закачивается в соляной пласт, обогащается солью, затем проходит сложную процедуру очистки, а отработанный рассол вновь возвращается в шахту, - рассказывает автор идеи главный химик предприятия Александр СЕЛЕЗНЁВ.- Суть технологии ещё и в том, что в скважине идёт доочистка этого рассола от различных примесей, например кальция, магния, которые раньше нужно было где-то хранить. Теперь они остаются под землёй, и для скважины это хорошо, потому что она постепенно заполняется и не будет пустой.
Технология оказалась выгодна не только экологически, но и экономически, потому что дала колоссальную экономию энергии, а также значительно сократила расходы на содержание оборудования.
Ртуть ушла в прошлое
Ещё одно, без преувеличения, выдающееся достижение «Саянскхимпласта» в области экологии - запуск мембранного электролиза, который в российской химической отрасли осуществили впервые.
- Раньше это было ртутное производство хлора и каустической соды, - объясняет Александр Селезнёв. - Здесь стояли 96 немецких электролизёров, в которых обращалось огромное количество очень опасного ядовитого вещества. Поэтому у нас всегда было желание перейти на безопасную и экологичную технологию.
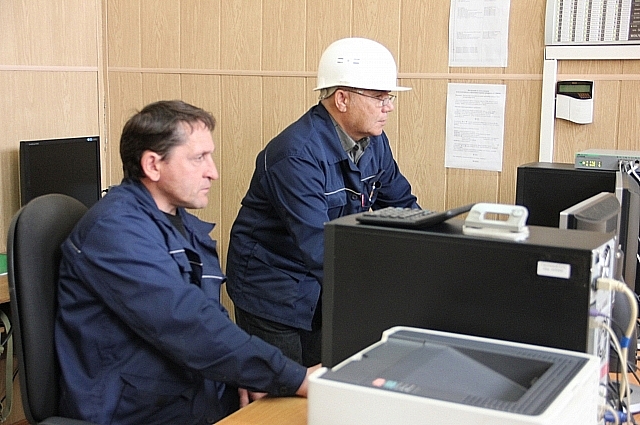
Чтобы объяснить, какую опасность представляли ртутные электролизёры, специалист рассказал о ситуации, сложившейся в своё время в японской области Минамато, где существовало химическое производство с применением ртути, отходы которого сбрасывали в море. Через какое-то время в этой области стали регистрировать странные явления: сначала у кошек, а потом и у людей начинались непроизвольные подёргивания мышц, а затем наступал летальный исход. Когда выяснили причину заболевания, а оказалось, что ртутные отходы по цепочке усваивали рыбы затем животные и люди. По всей Японии закрыли ртутные производства и позднее именно там зародилась новая технология - мембранный электролиз, который в 2006 году ввели в эксплуатацию на «Саянскхимпласте». На сегодняшний день он считается самой передовой технологией и самым безопасным методом производства хлора в мире.
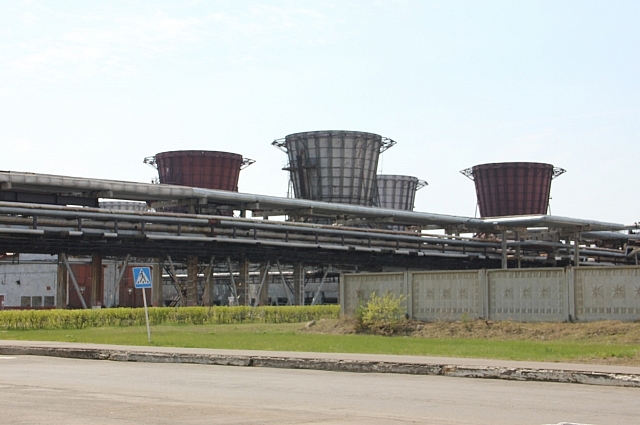
Кроме того, реализация данного проекта позволит полностью обеспечить выпуск ПВХ хлором собственного производства, а также снизить его себестоимость.
В технологический процесс производства поливинилхлорида на саянском предприятии внедрены и другие уникальные для российского химпрома ноу-хау. Среди них - германская установка выпаривания серной кислоты, которую применяют для сушки газообразного хлора. Это оборудование из борсиликатного стекла, в нашей стране не производящееся, обеспечивает замкнутый цикл использования вредного вещества и таким образом не просто решает проблему его хранения, но и снижает потребление серной кислоты на предприятии в тридцать раз!
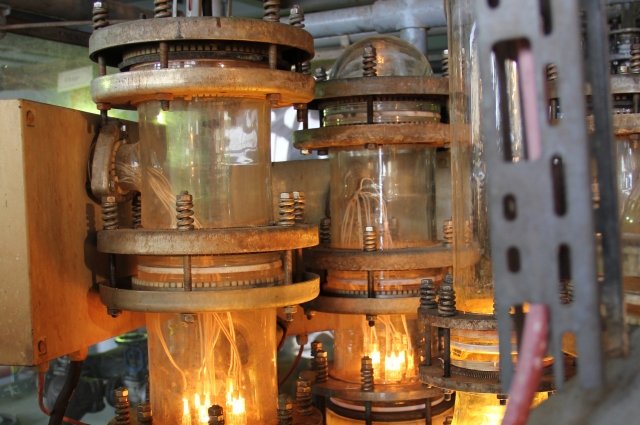
- Сейчас котельная вырабатывает до 20% пара от общего объёма, потребляемого на заводе, - говорит Александр Селезнёв. - А это, в свою очередь, позволяет не только существенно экономить средства, но и значительно снижает выбросы в атмосферу углекислого газа, образующегося при сжигании угля.
С парниковым эффектом борется и новая печь крекинга, где непосредственно производится винилхлорид. Она построена по немецкой технологии и запущена в эксплуатацию в феврале 2011 года.
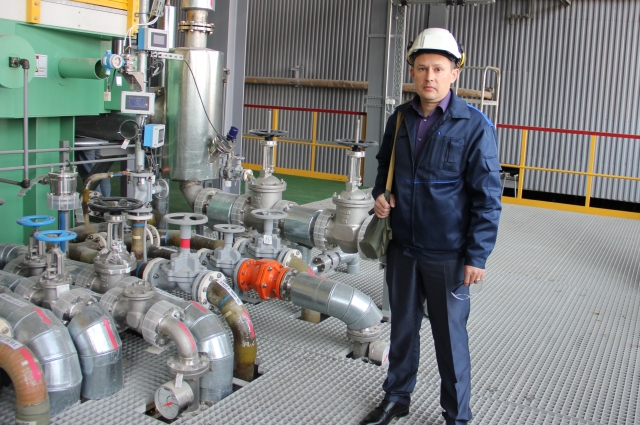
![]() |
---|
Андрей Куприн |
- В России таких установок больше нет, - говорит начальник производства поливинилхлорида Андрей КУПРИН. - Она уникальна с точки зрения экологии: если в старых печах температуру, необходимую для технологического процесса, создаёт жидкое топливо, то в новой горит газ, в результате чего выбросы углекислого газа в атмосферу на 30% ниже, чем в старых печах. Кроме того, здесь применяется так называемая энергохимическая технология: то есть печь не только производит химический продукт, но ещё и потребляет для этого собственную энергию.
Дело - за газом!
Проектная мощность «Саянскхимпласта» - 250 тысяч тонн поливинилхлорида в год. Но выйти на неё предприятие смогло только в 2005 году. В результате проведённой модернизации в настоящее время завод выпускает 280 тысяч тонн ПВХ в год.
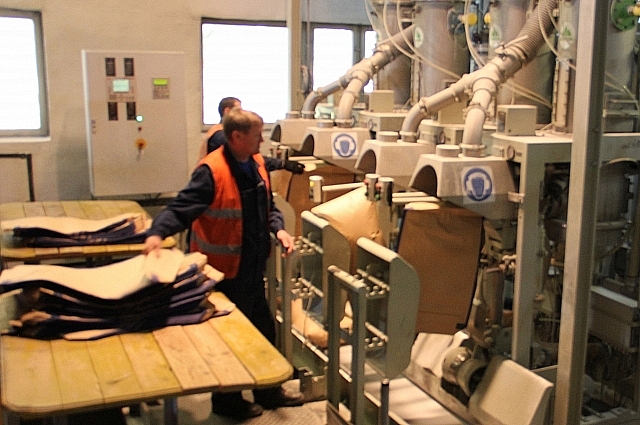
Несмотря на то что в России есть ещё два крупных предприятия аналогичного профиля - в Стерлитамаке и Волгограде, российский рынок обеспечен этим продуктом только на 50%, причём половину этого объёма производят в Саянске. Остальное завозится из-за границы.
- Мы уже сейчас готовы производить 350 тысяч тонн ПВХ, а при дальнейшей реконструкции - более 400 тыс. тонн, - утверждает генеральный директор Николай Мельник. - Единственное, что нас сдерживает, - недостаток сырья - этилена, ещё одного кроме соли необходимого компонента для производства поливинилхлорида. Правда, нефтяники обещают до 2030-го дать стране 6 млн тонн этилена, но если бы они были поближе к нам…
Как говорят химики, сегодня самое экономически и экологически выгодное углеводородное сырьё для производства ПВХ - газ. К примеру, весь американский поливинилхлорид производят только из газа. В России же пока - только из нефти.
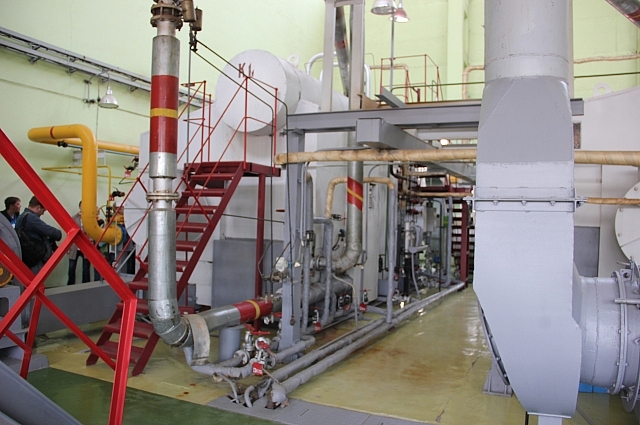
- Но мы уверены, что наша совместная работа с нефтяниками и энергетиками, а также визит президента России в Китай дадут толчок развитию Ковыкты и Чаянды, у нас появится сырьё и наше предприятие ещё больше увеличит те 48% российского рынка в мире, которые мы занимаем, - уверен Николай Мельник. - К тому же, в СМИ сообщили, что контракт на поставку газа в Китай готов на 98%. Я думаю, что ждать подписания этого документа осталось недолго, после чего начнётся очень динамичная работа по его реализации. И газопровод «Сила Сибири», который планируется построить в ближайшие годы и по которому в Юго-Восточную Азию станут поставлять порядка 63 млрд кубов газа, будет иметь ответвления и к нам. Потребители на этот газ есть, его нужно только привести.